Share This
Related Posts
Tags
Printing a Building
By Anca Gagiuc on Oct 1, 2015 in Technology
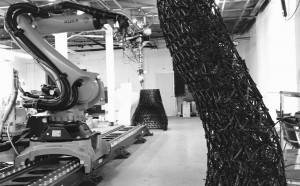
Robot and wall build with Branch, courtesy Branch Technology.
The 3D printing technology continues its adventure, conquering industry after industry. Among the latest highly debated upon is the construction industry and the upgrades 3D printing brings to it. It’s no surprise as construction is a $1 trillion industry in the United States ($8.5 trillion worldwide) and accounts for 8-10% of the U.S. GDP.
Startup Branch Technology of Chattanooga, Tennessee, led by visionary Platt Boyd, came up with a new approach inspired by nature. The company announced at GIGTANK, a boutique accelerator for startups developing high-bandwidth business applications, that it is the first company to successfully construct building walls at scale using the world’s largest freeform 3D printer; they are the winners of the Investor’s Choice Award.
Branch’s mission is to simplify the work of architects by giving them more freedom to incorporate new geometries into their designs, inspired by nature. Like bones in our body or trees in the forest, optimized geometries are made strong and functional by the material filing the matrix. After that, the interior and exterior skins can be finished in any way.
To achieve that, Cellular Fabrication™ (C-Fab™) was designed as Branch’s patented freeform 3D printing process. It turns the question “how much can we build?” into “how little can we build?” Freeform printing in open space is freed of the slow, layer-by-layer build process of traditional 3D printing. They’ve came up with an algorithm which creates both the geometry and robotic motion to construct complex geometries in open space, saving on the use of support materials and on highly controlled build environments.
The technology uses a 12-and-a-half-foot Kuka robotic arm which travels on a 33-foot rail to build a simple lightweight scaffolding made out of ABS plastic reinforced with carbon fiber. Then, using the same tools that contractors use today, denser materials are added on it, like spray foam, dry wall, stucco, concrete, increasing the strength and integrity of the overall structure. Using this system, each wall is custom-made and can curve or slope as the architect desires.
“When geometry is not an issue, you can do almost anything,” Branch founder and CEO Platt Boyd said at the startup’s headquarters in Chattanooga. “If an architect can send us an original design file we can fabricate that.”
According to the company, a two-and-a-half-pound 3D printed matrix with spray foam applied can support almost 3,000 pounds. One of the most attractive features of Branch Technology is related to construction costs which drop to somewhere between $80 and $140 per square foot. This compared to the thousands of dollars it costs to build big buildings with creative designs makes the startup highly viable.
Boyd himself is an award-winning architect with LEED credentials and 15 years of experience seasoned at Seay, Seay & Litchfield Architects in Alabama where he mainly did architectural work for universities, the Department of Defense, and a few house contractors. He left the firm in 2014 and recently moved to Chattanooga to work out of INCubator, one of the nation’s oldest incubators. In the same building other startups are using 3D printing in new ways, creating more and more things, from shoes to sensors.
Branch Technology also announced that it will sponsor the world’s first design contest to 3D print a home. It will start in September and culminate with a $10,000 prize and the construction of a 3D printed home in Chattanooga.